(GTC) Diagnosing Problems with Plug-In Modules (3047G Module) - Troubleshooting
(GTC) Diagnosing Problems with Plug-In Modules (3047G Module)
Article Type:
|
Applicable Equipment:
|
Troubleshooting
|
AM3047G signal conditioner module
|
Error Description:
The most common issue with the module is an improper reading being outputted from it. Another potential issue is a failing self-test.
This guide is specifically for GTC machines; for older systems, DSI should be contacted directly for assistance. This guide also assumes the issue has been isolated to the module itself, and as such does not discuss troubleshooting the load cell, instrument module, embedded computer, or any additional components or wiring.
Possible Error Causes:
An improper reading could be due to any number of failing/loose components, damage to the traces, bent/damaged pins at the rear of the module, or incorrect jumper settings. Self-test failure could be due to failing/loose components or damage to the traces, as well. A few other potential, minor issues with the module will also be discussed.
Warning and Cautionary Statements:
Review and understand all warning and caution statements before proceeding:
- multimeter
- flat-head screwdriver
- Schroff extender card
- pliers
- soldering iron
- solder
- desoldering wick/braid or desoldering pump (solder sucker)
- wire cutters (diagonal cutters)
- ESD grounding strap
Troubleshooting Flow Chart:
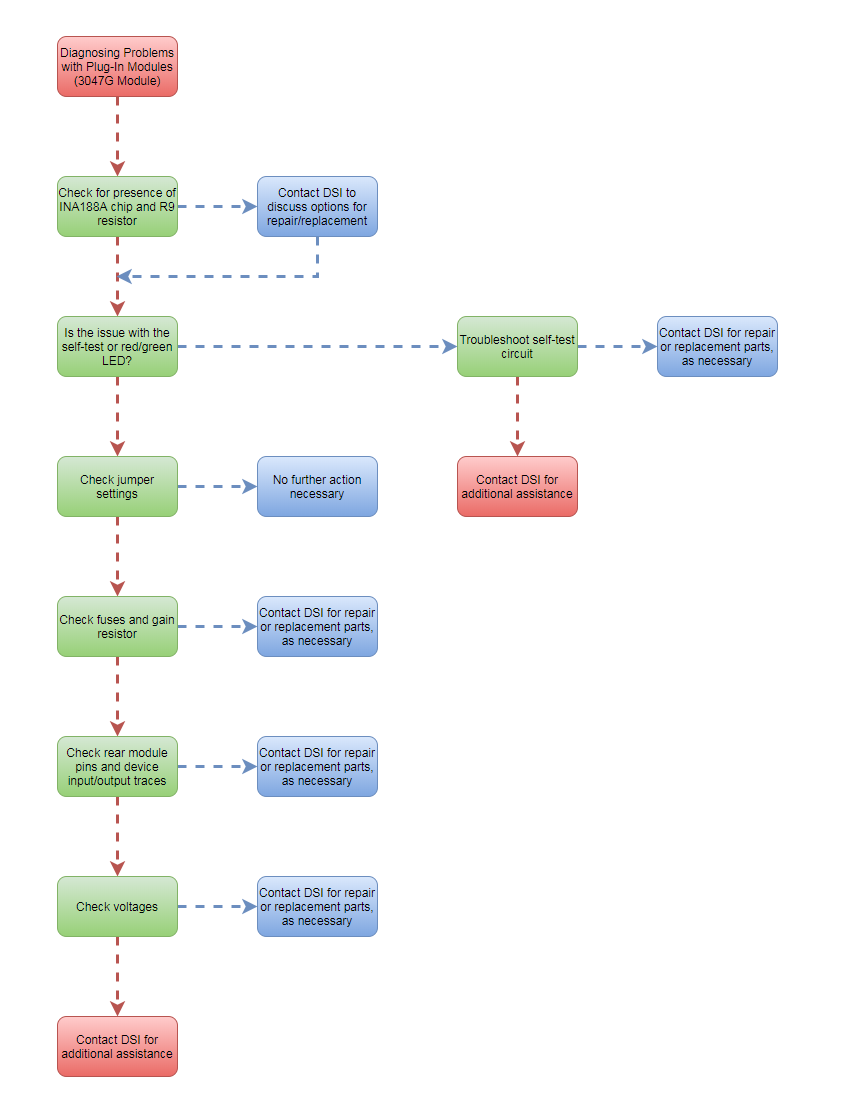
Troubleshooting Steps:
Check for presence of INA188A chip and R9 resistor:
Before starting the real troubleshooting, the instrumentation amplifier chip should be checked to make sure it's the correct one. The old instrumentation amplifier chip from Series 3 was sensitive to noise introduced by elements within the GTC console. The noise manifested itself as a small but consistent spike on Force data. The old instrumentation amplifier was replaced by INA188 to remedy this issue. While it is unlikely to be the cause of the issue(s) necessitating perusal of this troubleshooting guide, it is worthwhile to check while the signal conditioner module is being investigated.
To check for the presence of the INA188 chip and resistor R9:
- Take a look at the chip indicated in the picture below. If it is the correct chip, 'INA188' will be indicated on the top face, but it may be difficult for some to see. As long as it resembles the one in the picture below (i.e., is a SOIC on a SOIC-to-DIP adapter), that is sufficient. It does not matter if the adapter board is some color other than green (it is commonly red, for instance). The predecessor INA118 chip is indicated in the second photo below. That is NOT the chip you want on your board in a GTC based Gleeble system.
INA188 chip on its adapter board
INA118 chip
- Next, check for the presence of resistor R9 (see the picture below). It had a few uses in older versions of the AM3047, but should not be populated on the AM3047G. If it is present, use wire cutters (diagonal cutters) to remove it. You will have to cut it off, so be certain you are looking at the correct resistor before doing so. Alternatively, you could use a soldering iron and either desoldering wick/braid or a desoldering pump to remove it, if that is something you are comfortable doing.
If the instrumentation amplifier chip is an INA188, proceed to 'Is the issue with the self-test or red/green LED?'. If it is not an INA188, notify DSI of this issue so we can begin planning how to rectify the situation. Regardless of whether the entire module is replaced or just the instrumentation amplifier chip, the module will have to be recalibrated. Once DSI has been notified, proceed to 'Is the issue with the self-test or red/green LED?'.
Is the issue with the self-test or red/green LED?:
Depending on whether the issue is related to the self-test or the reading from the device under normal operation, the troubleshooting steps to follow will differ significantly. This guide assumes the issue has already been identified, and as such this step serves only as a point of divergence for the two troubleshooting paths.
If the issue pertains to the self-test or the red/green LED on the front of the module, proceed to 'Troubleshoot self-test circuit'. If the issue pertains to the reading of the device under normal operation, proceed to 'Check jumper settings'.
Troubleshoot self-test circuit:
The self-test checks whether there has been some appreciable drift in the transducer reading since the last time that the module was calibrated. This is done with a zero-value check and an upscale-value check, which both supply predetermined inputs to the transducer and check the output against values stored in the module's EEPROM chip. In the case of AM3047G modules, the zero-value check does not actually change the input to the load cell, because it assumes the load cell will read near zero when unloaded. This is why there must be nothing between the jaws when performing the self-test. If the load cell is pre-loaded, it will likely fail the self-test. The upscale-check closes a relay which alters the overall resistance between one of the excitation inputs and one of the signal outputs, resulting in an upscale reading. If those checks are within given tolerances of the values stored in the EEPROM, the self-test has passed, and the LED on the front of the module turns green. If either one is outside the tolerances, the self-test has failed and the LED turns red. This step will check several components vital to the overall readings, as well as the LED itself.
Caution: Damage to electrical components can result if proper electrostatic discharge (ESD) prevention protocols are not followed.
To troubleshoot the self-test circuit:
- Power down the Gleeble system, and ground yourself so as to protect the module from ESD. Remove the AM3047G module from the console. Remove the metal covers, and visually examine IC7 and IC9 (indicated in the photo below). These are the EEPROM chip and the I2C I/O expander chip, respectfully. Check for any bad solder joints. Also try pushing or pulling on the chips lightly, to see if they are loose. If you find any issues here, and if you are comfortable, use a soldering iron to repair the joints.
- Locate resistor R2 on the module (see picture below). Using a multimeter set to measure resistance, check the resistance across R2. It should be roughly 30,000 ohms. if it is significantly different, use pliers to remove it from the module and check it again by itself. If the resistor has been identified as faulty, it needs to be replaced. This resistor is an essential part of the upscale check, so if something has happened to it since the last calibration, it will likely cause the upscale check to fail.
- Locate resistors R18 and R19 on the module (see picture below). Using a multimeter set to measure resistance, check the resistance across each one. They should both be roughly 470 ohms. They are part of the LED circuit, so if either one has failed, the LED may not illuminate properly.
- The final check will be to ensure that the various components in this circuit are getting the proper supply voltage. To do this, you will first have to place the module on the extender card (shown below), plug the extender card into the correct slot in the console, and power the Gleeble back up.
Schroff extender card
- Once the Gleeble is powered back up (either Configuration Mode or Run Mode is adequate for these checks), set your multimeter to measure DC voltage, and plug the common lead into the black test point on the front of the module.
module test points
- For IC7, connect your positive lead to pin 8. Use the two photos below to determine which pin that is. There should be +5 volts at pin 8.
EEPROM chip pin configuration
EEPROM chip with index signifying location of pin 1
- For IC9, connect your positive lead to pin 16. Use the two photos below to determine which pin that is. There should be +5 volts at pin 16.
I2C chip pin configuration
- Locate RL1 (see the photo below). RL1 is the relay which is closed during the upscale check. Connect your positive lead to pin 2 of RL1. Use the second photo below to determine which pin that is. There should be +5 volts at pin 2.
Relay chip pin configuration
- If any of these three checks have failed, that may indicate a bad trace on the board. If all three have failed, that suggests the voltage regulator supplying the +5 volts to them is perhaps not working properly. Locate IC3 (see the photo below). This is that +5V regulator for those other components. Using the photo below as a reference, connect your positive lead to pin 1. There should be +5 volts at pin 1. If there is not, check pin 3; that should be +15 volts.
+5V Regulator chip pin configuration
If this step indicated an issue that has been addressed and the self-test is now working properly, there is no need for further action. if it indicated an issue that you were unable to resolve yourself, contact DSI to discussing repairing or replacing the module. If these checks didn't indicate any issues, contact DSI for further troubleshooting support.
Check jumper settings:
The AM304x signal conditioner module has multiple iterations because of the varying transducers it needs to be able to interface with (load cells, LVDT-based gauges, etc). It is configured with different components based on the transducer it is interfacing with. Jumpers play a crucial role in this configurability. If they are not set correctly, the module will not read the signal from the transducer properly.
Caution: Damage to electrical components can result if proper electrostatic discharge (ESD) prevention protocols are not followed.
To check the jumper settings:
- Power down the Gleeble system, and ground yourself so as to protect the module from ESD. Remove the AM3047G module from the console. Remove the metal covers. Identify the nine jumper locations on the module, as indicated in the photo below, and check the presence/absence of the jumpers against the chart below.
Jumper
|
AM3047G Setting
|
J1
|
IN
|
J2
|
IN (Bottom 2 Pins)
|
J3
|
IN
|
J4
|
IN (do NOT install for low-force load cells)
|
J5
|
OUT
|
J6
|
OUT
|
J7
|
IN
|
J8
|
IN (Left-Most 2 Pins)
|
J9
|
IN (Right-Most 2 Pins)
|
- As mentioned above, the J4 jumper should be present so long as the module is not being used with a low-force load cell. If it is being used with a low-force load cell (LForce2k, LForce5k, etc), ensure that this jumper is removed from the module or the excitation voltages for the load cell will not be correct.
jumper locations
If the jumper settings were incorrect, and correcting them has resolved the issue, there is no need for further action. If the issue is still present, proceed to 'Check fuses and resistors'.
Check fuses and gain resistor:
The excitation voltages pass through two fuses before leaving the module and heading out to the load cell. If those fuses are blown, the load cell will not function properly. The resistance of the gain resistor is also worth checking, at this point.
Caution: Damage to electrical components can result if proper electrostatic discharge (ESD) prevention protocols are not followed.
To check the fuses and gain resistor:
- Locate the fuses in question (see the picture below). Make sure they are populating the locations indicated in the picture. If not, use pliers to remove them and relocate them to the correct positions. They should come out of their sockets without much difficulty.
- Using a multimeter set to measure resistance, check the resistance across the fuse. It should be some small value around 1 ohm. if it is significantly different from that, use pliers to remove it from the module and check it again by itself. If the fuse is blown, the multimeter will indicate an 'open lead (OL)'.
- Finally, locate resistor R1 (see the picture below). This is the gain resistor, and if there is something wrong with, that will have major implications on the reading coming out of the module. Using a multimeter set to measure resistance, check the resistance of R1. It should range between 150 ohms - 360 ohms, depending on the size of the load cell it is interfacing with. if it is significantly different, use pliers to remove it from the module and check it again by itself. If the resistor is found to be faulty, it will need to be replaced and the module recalibrated by DSI personnel.
If there is a faulty fuse or resistor, contact DSI to discuss replacing it. Note that if R1 is faulty, replacing that may necessitate recalibrating the module. If these checks didn't indicate any issues, proceed to 'Check rear module pins and device input/output traces'.
This step will attempt to verify that the input and output signals are properly continuous across the module. The excitation voltages, which are the inputs to the load cell, start at transistors Q1 and Q2 before passing through the pins at the rear of the module, into the backplane and beyond. The output signals from the load cell enter the module at the rear module pins and ultimately go into the INA188 instrumentation amplifier. If these signals are lost at any point along the way, the reading is not going to be correct.
Caution: Damage to electrical components can result if proper electrostatic discharge (ESD) prevention protocols are not followed.
To check the rear module pins and device input/output traces:
- Take a look at the pins at the back of the module, keeping an eye out for bent or missing pins. Notice also the 'B' and 'A' designations above the two columns of pins.
rear module pins
- Pins B18 and B22 carry the excitation voltages, while B30 and B32 carry the load cell output signals. Check if any of those 4 pins are bent or missing at the rear of the module.
rear module pins
- Identify Q1 and Q2 on the module (see picture below).
- Assuming the pins are there as expected, set your multimeter to measure resistance, and check the continuity from those rear pins to Q1, Q2, and the INA188 chip using the table below.
Rear Module Pin
|
Component Pin
|
B18
|
Q1, pin 3 (top pin)
|
B22
|
Q2, pin 3 (top pin)
|
B30
|
INA188, pin 3 (third from top on right side)
|
B32
|
INA188, pin 2 (second from top on right side)
|
Q1 and Q2 Pin Configuration
INA188 Pin Configuration
- There is a horizontal line on the INA188 chip which serves as a visual indication of which side of the chip pins 1 and 8 are on. If the chip is oriented on the adapter board properly, the horizontal line will be near the top.
- FS1 (one of the fuses identified in the previous step; the right-most one) is the only component between B18 and Q1, so if there is no continuity between B18 and Q1, make sure FS1 is making good contact. If it is, and there is still no continuity, the trace from B18 to Q1 must be damaged somewhere.
- FS2 (one of the fuses identified in the previous step; the second one from the right) is the only component between B22 and Q2, so if there is no continuity between B22 and Q2, make sure FS2 is making good contact. If it is, and there is still no continuity, the trace from B22 to Q2 must be damaged somewhere.
- There are no components between B30 and INA188 or B32 and INA188, so if there is no continuity in either case then the corresponding trace must be damaged somewhere.
If there was a bent pin, and straightening it has resolved the issue, there is no need for further action.. If there is a missing pin or a damaged trace, contact DSI to discussing repairing or replacing the module. If these checks didn't indicate any issues, proceed to 'Check voltages'.
Check voltages:
There are quite a few components involved in providing the excitation to the load cell and then conditioning the signal from the load cell. This step will have you check as many of these components' input, output, and/or supply voltages as is practical to.
Caution: Damage to electrical components can result if proper electrostatic discharge (ESD) prevention protocols are not followed.
To check the voltages:
- First, place the module on the extender card, plug the extender card into the correct slot in the console, and power the Gleeble back up. Once the Gleeble is powered back up (either Configuration Mode or Run Mode is adequate for these checks), set your multimeter to measure DC voltage, and plug the common lead into the black test point on the front of the module.
- Locate IC1 (see the photo below). IC1 is the +15V regulator for the module. Using the photo below as a reference, connect your positive lead to pin 3. There should be +15 volts here. If there is not, check pin 1; that should be +18 volts.
+15V Regulator chip pin configuration
- Locate IC2 (see the photo below). IC2 is the -15V regulator for the module. Using the photos below as a reference, connect your positive lead to pin 3. There should be -15 volts here. If there is not, check pin 2; that should be -18 volts.
-15V Regulator chip pin configuration
-15V Regulator chip with index signifying location of pin 1
- Locate IC6 (see the photo below). IC6 is a precision voltage reference chip, used in both the upscale check (for other modules) and providing excitation voltage to the load cell. Using the photos below as a reference, connect your positive lead to pin 6. There should be +5 volts here. If there is not, check pin 2; that should be +15 volts.
Voltage Reference chip pin configuration
- Locate IC4 (see the photo below). IC4 is a collection of 4 operational amplifiers, used in providing excitation voltage to the load cell. Using the photos below as a reference, connect your positive lead to pin 4. There should be +15 volts here. Next, check pin 11; that should be -15 volts.
Quad Op Amp chip pin configuration
- Locate Q1 (see the photo below). Q1 is a transistor, and is the component which actually outputs the positive excitation voltage for the load cell. Using the photos below as a reference, connect your positive lead to pin 3. There should be +8 volts here, unless this module is for a low-force load cell (LForce2k, LForce5k, etc), in which case there should be +5 volts. If there is not, check pin 2; that should be +15 volts.
Excitation Voltage Transistor chips pin configuration
- Locate Q2 (see the photo below). Q2 is a transistor, and is the component which actually outputs the negative excitation voltage for the load cell. Using the photos below as a reference, connect your positive lead to pin 3. There should be -8 volts here, unless this module is for a low-force load cell (LForce2k, LForce5k, etc), in which case there should be -5 volts. If there is not, check pin 2; that should be -15 volts.
Excitation Voltage Transistor chips pin configuration
- Locate IC8, the INA188 instrumentation amplifier mentioned earlier. There is a line on the topside of the chip which designates that end as the one closer to pins 1 and 8. Using that information and the photos below as a reference, connect your positive lead to pin 7. There should be +15 volts here. Next, check pin 4; that should be -15 volts.
INA188 chip pin configuration
- Locate IC5 (see the photo below). IC5 is a multiplexer, which is used during both the self-test and normal operation, and is the device which determines which of those sets of values is being outputted from the module to the instrument module. Using the photos below as a reference, connect your positive lead to pin 14. There should be +15 volts here. Next, check pin 3; that should be -15 volts.
Multiplexer chip pin configuration
if this step indicated an issue with any of the components, contact DSI to discussing repairing or replacing the module. If these checks didn't indicate any issues, contact DSI for further troubleshooting support.