(Series 3/GTC) LVDT-Based Gauge Only Reading Half Scale - Troubleshooting
Article Type:
|
Applicable Equipment:
|
Troubleshooting
|
39010:: +/- 6.35 mm Crosswise Transducer
|
|
39018:: +/- 2.54mm Crosswise Transducer
|
|
39050: +/- 12.7mm Lengthwise Transducer
|
|
39057:: +/- 25.4mm Hydrawedge Lengthwise Gauge
|
|
39060: +/- 12.7mm Lengthwise Hot Zone LVDT
|
|
59901: : +/- 62.5mm Stroke LVDT
|
|
59910: : +/- 18mm Hydrawedge Stroke
|
|
59921: +/- 50.8mm Stroke LVDT (3180)
|
Error Description:
The reading of an LVDT-based device only covers half of the expected range; generally the reading will stay on one side of the zero point. An example would be a CGauge is plugged in, but it only reads from 0mm to +6.35mm, rather than from -6.35mm to +6.35mm.
Possible Error Causes:
This issue occurs when a portion of the LVDT's secondary circuit is not functioning properly, and may be caused by a damaged gauge, loose connection, or problem with the signal conditioner module (or external oscillator/demodulator, if applicable).
Warning and Cautionary Statements:
Review and understand all warning and caution statements before proceeding:
- Digital Multimeter
- Flat-head screwdriver
- SAE allen wrench set
- Schroff extender card
- ESD grounding strap
Troubleshooting Flow Chart:
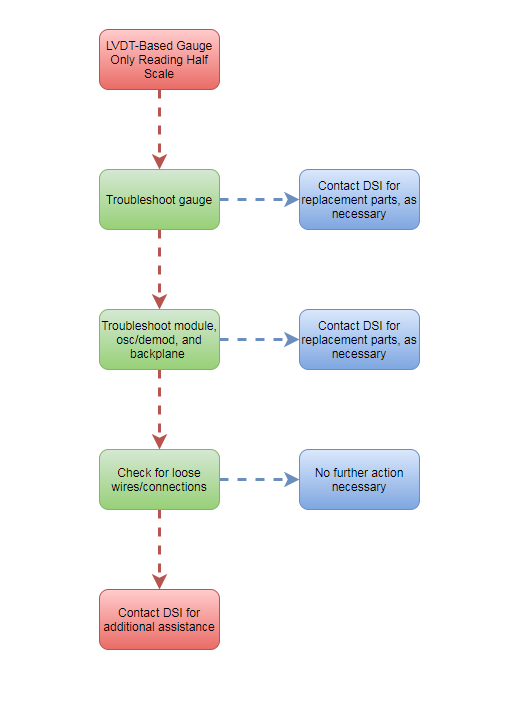
Troubleshooting Steps:
Troubleshoot Gauge:
The first step will be to rule out or identify a problem with the gauge itself. Its possible for the internal components of a gauge to be damaged, particularly if it's one of the gauges that mounts inside the vacuum tank. A gauge could also have a loose or damaged wire which, again, is more common in the gauges that are being routinely moved in and out of the vacuum tank.
For the purpose of this article it will be useful to know which gauges are considered 'fixed' in position and which are considered 'removable'. The table below displays this information:
Gauge Model
|
Gauge Description
|
Fixed or Removable
|
59901
|
+/- 62.5mm Stroke LVDT
|
Fixed
|
59910
|
+/- 18mm Hydrawedge Stroke LVDT
|
Fixed
|
59921
|
+/- 50.8mm Stroke LVDT (Gleeble 3180)
|
Fixed
|
39010
|
+/- 6.35mm CGauge - Crosswise Transducer
|
Removable
|
39018
|
+/- 2.54mm Dilatometer - Crosswise Transducer
|
Removable
|
39050
|
+/- 12.7mm Jaw-to-Jaw Lgauge - Lengthwise Transducer
|
Removable
|
39057
|
+/- 25.4mm Hydrawedge Jaw - Lengthwise Transducer
|
Removable
|
39060
|
+/- 12.7mm HZT060 - Lengthwise Transducer
|
Removable
|
If troubleshooting one of the removable gauges, the easiest thing to start off with is to try swapping the gauge itself with a similar gauge and see if the problem still remains. To do this:
- Unplug the gauge in question
- Do not change the module being used
- Plug in one of the other listed 'removable' gauges into the same plug that the original gauge was attached to
- Actuate the new gauge by hand to see if the reading now displays full range
- Note that since the module did not change, a full-range reading will still be that of the original gauge. For instance, if the original troublesome gauge is a 39010 Cgauge that is replaced with a 39050 Jaw-to-Jaw Lgauge for troubleshooting purposes, you would expect to see a full-range reading of +/- 6.35mm and not +/-12.7mm.
- If the new gauge allows for a full-scale reading to be achieved, then the problem has been narrowed down to the original gauge. The next step would be to investigate the original gauge's wiring.
For both the removable and fixed gauges the next step is to check for loose/damaged wires at either end of the gauge, and repair any wiring issues found.
For removable gauges:
- Unplug the gauge from the Gleeble
- Open up the black plug that is found on the gauge
- Check for any detached wires and repair as needed.
For fixed gauges:
- Turn off all power to the Gleeble
- Locate the oscillator/demodulator that corresponds to the device in question. The locations of the oscillator/demodulators are shown below:
The Stroke external osc/demod is located within the load unit, inside this box
The Hydrawedge Stroke external osc/demod is located inside the MCU NEMA box
-
Acquire a multimeter and set it to measure electrical resistance
-
On the oscillator/demodulator, measure the electrical resistance across the primary and two secondary coils. If everything is correct, the measurements should be roughly equal to what is shown in the table below:
External oscillator-demodulator, with pin locations highlighted
Coil
|
Pins
|
Resistance
|
Primary
|
1-2
|
57 ohms
|
Secondary
|
3-4
|
110 ohms
|
Secondary
|
5-6
|
108 ohms
|
- If any of the resistance measurements are much lower than what is listed, the corresponding electrical circuit should be investigated for a short circuit
- If any of the resistance measurements are much higher than what is listed or open circuit, locate the LVDT itself and make sure the wires are all properly secured on that end.
Stroke LVDT
Hydrawedge Stroke LVDT
If a wiring issue was discovered and repaired, troubleshooting is complete.
If swapping gauges indicated that the issue lies with the gauge, but there's no evidence of wiring issues, contact DSI for further assistance
If these checks did not indicate an issue with the gauge itself, proceed to Troubleshoot Module, Osc/Demod, and Backplane.
Troubleshoot Module, Osc/Demod, and Backplane:
The signals from each LVDT go back through a signal conditioner module before passing through the backplane and finally the instrument module or toro board. If there is an issue with the signal conditioner module, oscillator/demodulator or backplane it may affect the final reading of the device. Common failures include a failed component or trace.
Caution: Damage to electrical components can result if proper electrostatic discharge (ESD) prevention protocols are not followed.
To troubleshoot the module, osc/demod, and backplane for removable gauges:
- Turn off all power to the Gleeble.
- Ground yourself using an ESD anti-static wrist strap to prevent damaging the module while working on it.
- Unplug the module that corresponds to the gauge in question from the Gleeble console.
- Remove the metal side covers of the module.
- Locate the oscillator/demodulator on the module. This is called a 'LVM-110'. The LVM-110 is shown in the picture below:
- The functionality of the LVM-110 can be investigated by replacing it with a LVM-110 found in a module that corresponds to one of the other removable gauges:
Note: Never adjust any of the potentiometers on the LVM-110. This will void the gauge's calibration
Note: Swapping the LVM-110 is only for troubleshooting purposes. Each LVM-110 is calibrated to a specific gauge. Using a gauge without its original LVM-110 during a test may result in inaccurate measurement readings.
- Remove the replacement LVM-110 from its parent module.
- Make note of the settings of switch 1 and 2 on the replacement LVM-110 so that the device can be returned to its original settings later.
- If necessary, adjust the settings of switch 1 and 2 on the replacement LVM-110 so that the settings match the LVM-110 that is to be replaced.
- Swap the original LVM-110 with the replacement LVM-110
- Power the Gleeble back on.
- Check to see if the gauge measurement now reads full-scale.
- If the measurement is still only capable of reading half-scale, power off the Gleeble. Return the LVM-110s to their original modules and reset the switches to their original settings.
- If the problem remains after swapping the LVM-110, unplug the original module from the Gleeble
- Locate the R30 resistor on the original module
- Use a multimeter to measure the resistance across R30
- The resistance of R30 should be roughly 47ohms
- The secondary signal going into the LVM-110 could be impacted if this resistor reading is not roughly 47ohms.
- If R30 is roughly 47ohms, there is still the chance that there is a bad trace on the module. To test this, use a multimeter and the photos below to check for electrical continuity across the following locations:
To
|
From
|
Pin B22 (module edge connector)
|
Right side of R30
|
Pin B24 (module edge connector)
|
LVM-110: Position 7
|
Pin B26 (module edge connector)
|
LVM-110: Position 8
|
Left side of R30
|
LVM-110: Position 6
|
Module Edge Connector Pinout
LVM-110 Pinout
- If the above continuity checks passed, locate the Schroff extender card. This is provided with every Gleeble system and is pictured below:
- Turn off all power to the Gleeble
- Plug the extender card into the backplane location that is normally occupied by the module and then plug the module into the extender card.
- Ensure the module and extender card are firmly connected
- Using a multimeter set to measure electrical resistance, check for continuity between positions on the LVM-110 and the phoenix connector on the backplane (see photo below). Be sure that the backplane phoenix connector you are looking at corresponds to the correct module slot.
To
|
From
|
Expected Resistance
|
Phoenix Connector: Position 3
|
LVM-110: Position 6
|
~ 48 Ohms
|
Phoenix Connector: Position 4
|
LVM-110: Position 7
|
~ 1 Ohm
|
Phoenix Connector: Position 5
|
LVM-110: Position 8
|
~ 1 Ohm
|
Backplane Phoenix Connectors
- If there is not continuity, double-check that the module, extender card, and phoenix connector are all pushed in fully.
- In the unlikely event that there is still not continuity, there could be an issue with the edge connector pins on the end of the module, the extender card, or the traces on the backplane. Check that the edge connector pins are not bent on the module.
Module Edge Connector Pins
To troubleshoot the osc/demod for the 59901 Stroke or the 59910 Hydrawedge Stroke fixed gauges:
- The fixed gauges do not have LVM-110s; instead, they have the external oscillator/demodulators mentioned earlier. The oscillator/demodulator that pairs with the 59901 Stroke and 59910 Hydrawedge Stroke are identical and therefore can be swapped for troubleshooting purposes. If the issue being experienced is with the 59901 Stroke or 59910 Hydrawedge Stroke and a Hydrawedge is available, this can be a useful action to take to narrow down the cause of the problem. To swap the oscillator/demodulators:
Note: Never adjust any of the potentiometers on the osc/demod. This will void the gauge's calibration
Note: Swapping the osc/demod is only for troubleshooting purposes. Each osc/demod is calibrated to a specific gauge. Using a gauge without its original osc/demod during a test may result in inaccurate measurement readings.
- Turn off all power to the Gleeble.
- Refer to the wiring diagrams provided with your Gleeble system when re-wiring the oscillator/demodulators.
- Consult the table below to determine which wiring diagram is applicable.
Gauge Model
|
Gauge Description
|
Wiring Revision
|
Drawing Number
|
59901
|
+/- 62.5mm Stroke LVDT
|
RevK
|
3000W30
|
|
|
RevJ
|
3000W24
|
59910
|
+/- 18mm Hydrawedge Stroke
|
RevK
|
3000W53
|
|
|
RevJ
|
3000W26
|
- Once the oscillator/demodulators have been swapped, check to see if the reading now goes full-scale or is still only half-scale.
If a nonfunctional component was identified (either module, LVM-110, external oscillator/demodulator, or backplane), contact DSI to discuss replacing the questionable part.
If issue was not resolved, proceed to Check for Loose Wires/Connections
Check for Loose Wires/Connections:
A number of issues could result if there is a loose wire or poor connection somewhere in the LVDT circuit.
Caution: Damage to electrical components can result if proper electrostatic discharge (ESD) prevention protocols are not followed.
To check for loose wires/connections:
- Power off the Gleeble system.
Warning: Before performing the following work, the Gleeble Load Unit and Hydraulic Pump must be de-energized and locked out and tagged out according to all local and facility regulations. Failure to do so could result in serious injury or death.
- Locate the relevant wiring diagram(s) for your gauge and wiring revision. These will be located in the Technical Reference Manual binder which shipped with the Gleeble system.
- The table below can be used as a reference to determine the pertinent wiring diagrams:
Gauge
|
Wiring Revision
|
Electrical Drawings
|
39010: +/- 6.35mm Crosswise Transducer /
38018: +/- 2.54mm Crosswise Transducer
|
Rev J
|
3000W20, 3000W25, 3000W30, 3000W38
|
|
Rev K
|
3000W32
|
39050: +/- 12.7mm Lengthwise Transducer/
39060: +/- 12.7 Lengthwise Hot Zone LVDT/
39057: +/- 25.4mm Hydrawedge Lengthwise Gauge
|
Rev J
|
3000W20, 3000W25, 3000W30, 3000W38
|
|
Rev K
|
3000W33
|
59901: +/- 62.5mm Stroke LVDT
|
Rev J
|
3000W24
|
|
Rev K
|
3000W30
|
59910: +/- 18mm Hydrawedge Stroke
|
Rev J
|
3000W26
|
|
Rev K
|
3000W53
|
59921: +/- 50.8mm Stroke LVDT (3180)
|
Rev E
|
3180W20
|
- Acquire a multimeter and set it to measure electrical resistance
- For each case, it is generally best to first measure from the backplane Phoenix connector to the where the gauge in question is plugged in/wired.
- If there is not continuity, check for loose wires all along the circuit path, as outlined by the wiring diagrams.
- Make note of and repair any faults encountered.
- The pictures below illustrate some of the common components referenced in the wiring drawings:
Gleeble ELCON
MCU Filter Plate
C-Strain and L-Strain Plugs
TBM3 is located inside the MCU lower I/O box
- Once all of the connections have been investigated, power the Gleeble back up to see if the fault has been corrected.
If investigating the wiring resolved the issue, no further action is necessary.
If investigating the wiring did not resolve the issue, contact DSI for additional assistance.